Summary:If you have decided to purchase an Injection Molding Machine for your company, there are some featur...
If you have decided to purchase an Injection Molding Machine for your company, there are some features that you should look for. Read this article for information on the different types of Injection Molding Machines, including Bakelite Injection Molding Machines, high speed Injection Molding Machines, and Energy Saving Injection Presses. We will also cover how to choose the best Injection Press for your business. Let's begin with Zhenfei.
high speed Injection Molding Machine
High speed injection molding machines have improved design, lubrication system, and service life. They can be used for both high-end and standard applications. They are also equipped with a servo motor feeding system to drastically reduce molding time. High-speed injection moulding machines are ideal for the packaging industry, and can be customized to meet the needs of different customers. For more information, please contact us. We will be glad to assist you in choosing the right high speed injection molding machine.
Injection speed has a direct impact on the molecular orientation of the component, its shrinkage, and the development of the joint line. When the injection speed is high, the part's material cools fast near the mold wall, which results in solidification in place and large differences in shrinkage. High injection speeds also improve surface quality and joint line strength, and reduce the risk of stress peaks and notch formation. If you're looking for a high-speed injection molding machine, consider these benefits.
A high-speed injection molding machine can deliver up to 360mm/s of injected plastic. This high-speed machine has an accumulator that helps to boost injection speed. The injection power is provided by a sensor MOOG servo valve. The machine has low-inertia injection mechanisms, which ensure a fast and stable platen location. These injection machines save electricity, energy, and other resources and are ideal for large-scale production.
Bakelite Injection Molding Machine
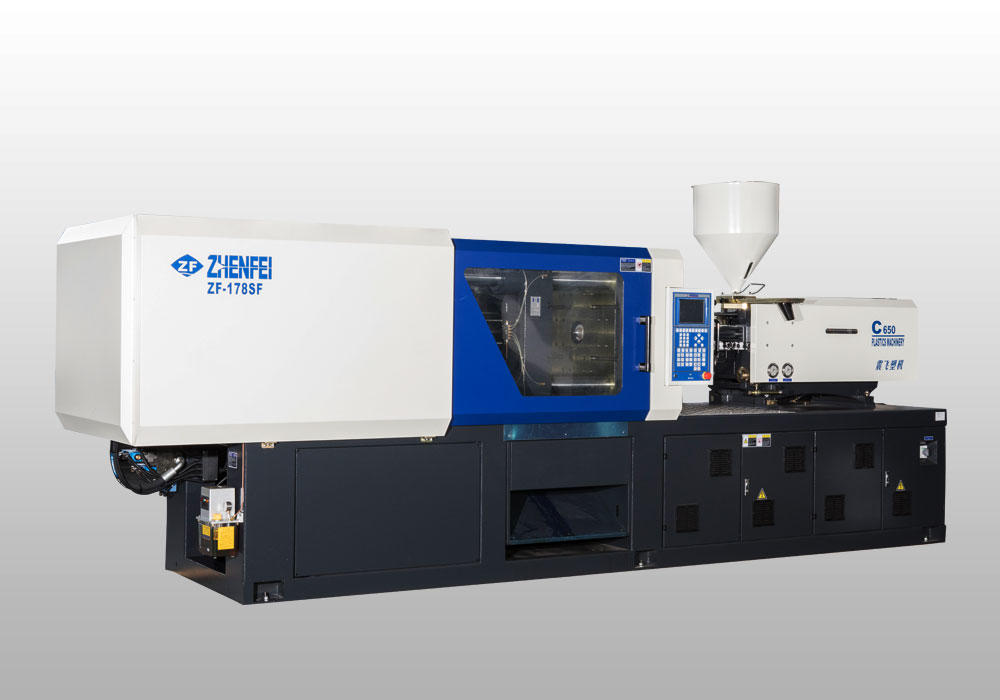
A BAKELITE INJECTION MOULDING MACHINE is ideally suited for medium-volume production. It has the flexibility and power to meet the requirements of the biggest companies. Moreover, bakelite plastic is highly resistant to varying temperatures and is suitable for a variety of industries. The Bakelite Injection Molding Machine is equipped with an automatic heating and cooling system. The heating process can be programmed so that the Bakelite Injection Molding Machine automatically switches on and off during the heating process.
The process of preparing the Bakelite injection mold begins with a temperature of 70-90°C. The injection screw shears and compresses the material before it is delivered into the mold. The temperature of the mold is then raised to 180°C. The resulting thermoplastic material is then melted and fused between the individual particles to form the Bakelite product. A Bakelite Injection Molding Machine can be configured to handle different thermoset materials and SMC materials.
Injection machine for bakelite moulds is available in two series: the U Series and the BAKELite horizontal. The former is fully automated, with a buzzer system. Both have their advantages. The U Series Bakelite Injection Molding Machine is an advanced model of the BAKELite horizontal injection molding machine. It has automatic heating and cooling process that allows it to be easily switched between different plastic materials. It is also equipped with a vacuum pump and a high-pressure system.
Energy Saving Injection Molding Machine
An Energy Saving Injection Molding Machine is one that uses less energy than a conventional one. Energy savings percentages are calculated by comparing the energy used by a new, energy-efficient machine function to the old, inefficient hydraulics. The energy used by an injection molding machine is divided into seven functions, which include plastification, barrel heating, platen movement, injection, clamping pressure, ejection, and barrel retraction. Conventional hydraulics use a standard induction electric motor with constant RPM, which powers 1-2 hydraulic pumps that run even when the machine is not in operation.
Injection molding machines that use an all-electric drive have reduced startup power and less maximum power consumption. They can also perform multiple operations simultaneously, and are characterized by shorter cycle times. Variable speed drives are also available to reduce power loss and improve process control. They also minimize the wear and tear on motors. Therefore, an Energy Saving Injection Molding Machine is a smart investment that is well worth considering. It will save you money while meeting your production needs.
A new generation of injection molding machines often offers significant energy savings over traditional hydraulics. Many manufacturers compare the new, energy-efficient machine functions to the old, inefficient hydraulics. Hydraulic oil is a small fraction of the cost of plastic injection molding machinery. However, making a small change to hydraulic oil can have dramatic impact on performance. With more energy efficient machines, manufacturing costs will decrease by more than three percent.