Summary:The selection of an injection molding machine is important for many reasons. A good choice will be e...
The selection of an injection molding machine is important for many reasons. A good choice will be efficient and will be cost-effective. The process can be quite complicated. There are many different types of machines and brands. The machines are usually classified according to tonnage, which is more precisely known as clamping force. This force is used to insert material into molds. The higher the tonnage, the bigger the machine will be. The machine will be designed to fit a certain plastic part and can be configured for various kinds of parts.
The process of injection molding involves a rotating screw that moves the mold material. There is a hydraulic system that applies pressure, which generally ranges from 100 to 150 MPa. After the injection, the pressure is released, and the part is released from the mold. The mold is then clamped shut for the next step in the process. The process takes a few minutes after each injection. If the time is too long, the part will not be ejected correctly.
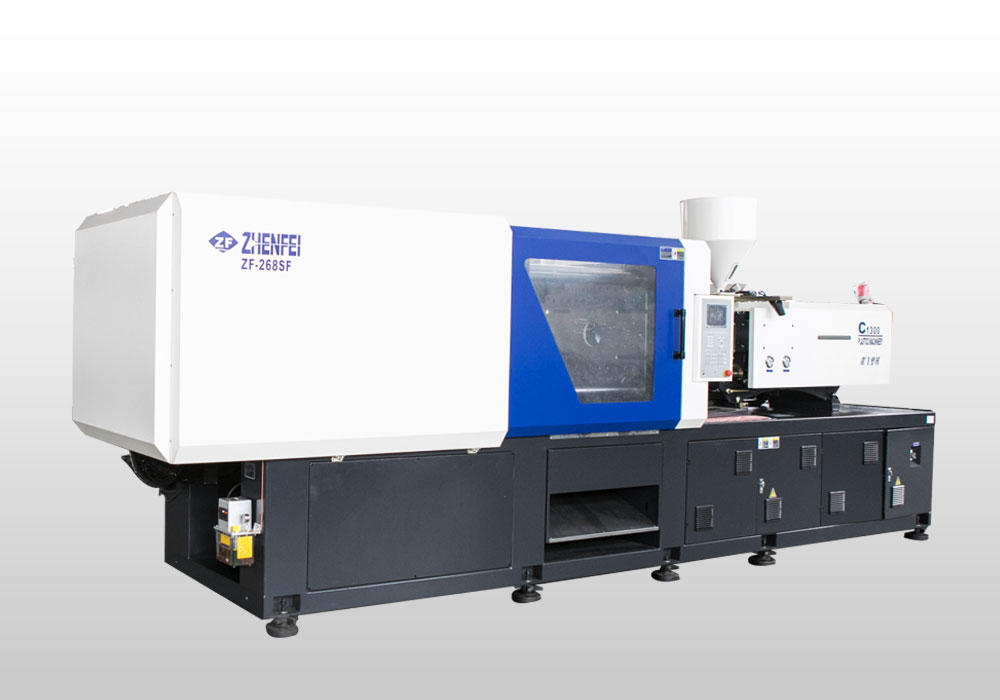
A hydraulic system in an injection molding machine allows the material to move continuously. The pressure is applied in the form of pressure. This pressure is usually between 100 and 150 MPa. After the part is ejected, the machine closes the mold and waits for the next injection. After a certain amount of time, the part cools and falls out of the mold. It is then ready to be ejected. The process can be repeated as long as the mold is cooled enough to accommodate it.
The clamping pressure is used to keep the mold closed during the injection. Too much or too little clamping pressure can cause flashing, which means excess material will surface on the part's edges. In addition to the clamping pressure, the viscosity of the plastic also affects its flow. This is measured by the MFI, or Melt Flow Index. The greater the MFI, the lower the risk of defect.
The
zf injection molding machine are able to handle different kinds of materials. It should be able to mold parts with very small wall thicknesses. Injection molding machines have a very high rate of production, which is a big advantage for many companies. These machines are an affordable way to produce high-quality and complex plastic components. If you are looking for an injection molding machine, EC21 is a good source of high-quality machinery at competitive prices.
The size and shape of the part should be within the specifications of the machine. The machine's clamp stroke and platen size determine the desired end product. The injection pressure is important for the mold's precision, as the toolmaker must take into account the end product's characteristics. The plastic injection molding machine should be able to mold small-sized parts as well. The platen and the clamp are very important factors. The plastic injection molding machines should be able to withstand the weight of these parts.
Injection molding equipments are typically self-regulating and automated. They rely on automation to inject materials into molds. They also usually cool the finished product autonomously. If you are looking for an injection molding machine, be sure to choose one that suits your needs. All of these factors will affect your production costs. You should consider the size and speed of your machine before you purchase it. A machine that can reduce cycle time and save you money on parts is a better choice.
Injection molding is a complex process. The parts produced are complex, and there are many variables that affect the process. The machine should be able to meet your needs and the requirements of your customers. Injection molding has many advantages, but the initial setup can be expensive. Then you'll need to find the right mold to fit your budget. If you decide to use a CNC-controlled injection molding machine, it is crucial to ensure that you choose the right model for the project.
The process of the injection molding machine requires post-processing. Once the part has been produced, the excess material will need to be removed. During this phase, the plastic will be solidified. It will be attached to the part. If the parts are complex, it will be molded from the raw material. It will require some post-processing before the parts are ready to be shipped to the end customer. The machine will typically need to eject the parts after each injection molding cycle.